The SCOM–model, short for Supply Chain Operations Reference, is the global standard for describing supply chain processes and improving performance. It is an open access, free of charge model that companies can use to set up processes properly and get a better grip on them. More than 5,000 companies worldwide use this model and more than 100,000 professionals worldwide are SCOM-trained. The model is in every logistics course, both in the Netherlands and internationally. This year the model has had its biggest update since its inception in 1996 and has now been made suitable for improving sustainability and circularity in the supply chain.
Introduction to processes
A process is a unique activity performed to meet predefined outcomes. The SCOM processes are those that a supply chain must execute in order to meet its primary objective of fulfilling customer orders. For each unique process, SCOM only has one representation. At the top of the SCOM Processes hierarchy is Orchestrate – a Level-0 process. Orchestrate is the only SCOM section that has a Level 0. The Level-0 process is at the Strategy level and informs and influences all of the levels below it.
After the Level-0 process, SCOM recognizes six major Level-1 processes — Plan, Order, Source, Transform, Fulfill, and Return.
Orchestrate supply chain
The Orchestrate Supply Chain process describes the activities associated with the integration and enablement of supply chain strategies. These include the creation of and management of business rules, performance management through continuous improvement, managing data, information, and supply chain technology, human resources management, contracts and agreements management, network design, regulatory and compliance management, risk management, Environment, Social, and Governance (ESG) management, enterprise business planning, segmentation creation and management, and circular supply chain management.
Plan
The Plan process describes the activities associated with developing plans to operate the supply chain. Planning is executed for the Order, Source, Transform, Fulfill and Return processes. These include determining requirements, gathering information about available resources, balancing requirements and resources to determine planned capabilities and gaps in demand or resources, and identifying actions to correct these gaps.
Functions: Chief Operations Officer, VP Supply Chain, Executive Director Supply Chain Planning, Supply Network Development Director, Demand Manager, S&OP Director, New Product & Clinical Supply Planning, VP Logistics, Site Director, Business Development Director, Vertical Industry Director, VP Commercial Relations, Operations Manager, Director Transport Management, Control Tower Lead, Director European Warehouse Network, Director Logistics Solutions, Global Logistics Director.
Order
The Order process describes the activities associated with the customer purchase of products and services, including attributes such as locations, payment methods, pricing, fulfillment status, and any other order data.
Functions: Chief Procurement Officer, VP Purchasing, Director Procurement, Supplier/Vendor Manager.
Source
The Source process describes the activities associated with procuring, ordering, scheduling the ordering, delivery, receipt, and transfer of products and/or services.
Functions: Supplier/Vendor Manager, Director Strategic Sourcing.
Transform
The Transform process describes the activities associated with the scheduling and creation of products (e.g., production, assembly/disassembly, MRO) and services.
Functions: Planning & Scheduling Officer, Scheduling Manager, Site Scheduler.
Fulfill
The Fulfill process describes the activities associated with fulfilling customer orders or services, including scheduling order delivery, picking, packing, shipping, installing, commissioning, and invoicing.
Functions: Chief Operations Officer, Plant Director, Manufacturing Director, Site Director, Regional Director Operations, Production Manager, Lean Program Director, WCOM / Lean Manager, Packaging Manager.
Return
The Return process describes the activities associated with the reverse flow of goods, services, and/or any service components from a customer back through a supply/service chain to diagnose condition, evaluate entitlement, disposition back into Transform or other circular activities.
Functions: Plant Director, Manufacturing Director, Site Director, Regional Director of Operations, Production Manager, Lean Program Director, WCOM / Lean Manager, Packaging Manager.
Levels
For each level-1 process, three or more differentiating level-2 processes exist. Each level-2 process contains level-3 process elements. These hierarchical relationships provide process classification. When conducting a SCOM project, SCOM users may decide to move some lower-level processes, such as those involving sourcing, delivery, and procurement, into other Process sections. SCOM can serve as a flexible and customizable model that can be applied to multiple industries and situations, so the framework process locations are not rigid. If this is done, SCOM users should be careful not to duplicate processes.
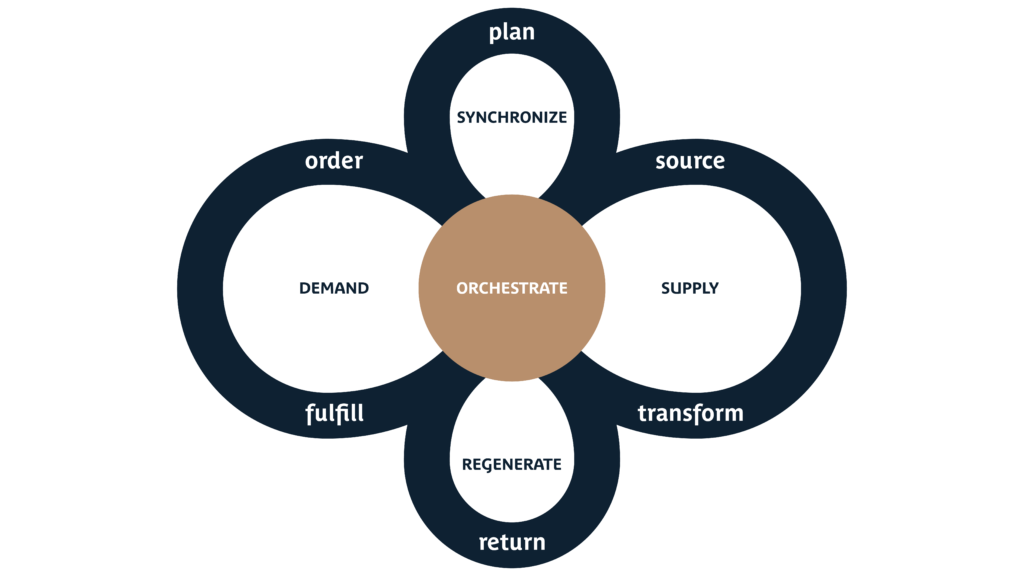